Vertical Light Path Vision Measurement System
A Vertical Light Path Vision Measurement System is an advanced optical system used primarily for precise measurement and quality control in various industrial and scientific applications. This system operates on the principle of light path analysis, where a vertical beam of light is utilized to measure the dimensions, shape, and surface characteristics of objects with a high degree of accuracy. The vertical orientation of the light path is crucial in enabling the system to handle a wide range of measurement tasks, particularly in environments where traditional horizontal systems may be limited due to space constraints or the nature of the objects being measured.
At its core, the Vertical Light Path Vision Measurement System consists of a light source, typically a laser or LED, which emits a focused beam of light vertically downward. The object to be measured is placed within the path of this beam. As the light interacts with the object's surface, it is either reflected, refracted, or scattered depending on the material properties and surface geometry of the object. A series of high-resolution cameras or optical sensors are strategically positioned to capture the light after it has interacted with the object. These sensors are capable of detecting minute variations in the light's path, intensity, and wavelength, which are then processed to generate precise measurements.
One of the significant advantages of this system is its ability to perform non-contact measurements. Unlike traditional measurement techniques that may require physical contact with the object, the Vertical Light Path Vision Measurement System relies solely on the interaction between light and the object's surface. This non-contact approach is particularly beneficial when dealing with delicate or soft materials that could be damaged by physical probing. Moreover, it allows for rapid measurements, making the system ideal for use in high-speed production environments where quick and accurate quality checks are essential.
The versatility of the Vertical Light Path Vision Measurement System is another key feature. It can be adapted to measure a wide variety of parameters, including thickness, height, flatness, and surface roughness. This adaptability is achieved through the use of different optical configurations and software algorithms tailored to the specific measurement task. For instance, when measuring the thickness of a transparent material, the system can be configured to analyze the refractive index changes as the light passes through the material. In contrast, for surface roughness measurements, the system might focus on analyzing the scattering pattern of the reflected light.
In addition to its versatility, the system is known for its high accuracy and precision. The optical sensors used in the system are capable of detecting sub-micron level deviations, making it possible to measure even the smallest imperfections on an object's surface. This level of precision is crucial in industries where tight tolerances are required, such as in semiconductor manufacturing, aerospace, and automotive industries. The high accuracy is further enhanced by advanced image processing algorithms that can filter out noise and compensate for any potential distortions caused by the optical setup.
Another important aspect of the Vertical Light Path Vision Measurement System is its integration with automated production lines. In modern manufacturing environments, the ability to perform inline measurements is increasingly important. The system can be integrated into existing production workflows, allowing for real-time quality control. This integration not only helps in detecting defects early in the production process but also reduces the need for post-production inspections, thereby improving overall efficiency. Additionally, the data collected by the system can be fed into a central database, enabling detailed analysis and traceability of the production process.
The design of the Vertical Light Path Vision Measurement System also considers environmental factors that might affect measurement accuracy. For example, temperature fluctuations, vibrations, and dust can introduce errors in the measurement process. To mitigate these effects, the system is often equipped with environmental sensors and stabilization mechanisms. These features help maintain the integrity of the measurement process by compensating for any external disturbances. In some cases, the system may also include a calibration routine that adjusts the optical setup periodically to ensure consistent performance.
From a usability perspective, the Vertical Light Path Vision Measurement System is designed to be user-friendly. The software interface typically includes intuitive controls and visualization tools that allow operators to set up measurements, view results, and make necessary adjustments with ease. Additionally, the system can be programmed to perform automated measurements, reducing the need for constant human intervention. This is particularly useful in large-scale production environments where hundreds or thousands of measurements need to be taken each day.
Furthermore, the system's data output is highly customizable. Depending on the application, the results can be presented in various formats, such as numerical data, graphical plots, or even 3D models. This flexibility in data representation allows for easy integration with other analysis tools and quality control systems. It also enables users to extract meaningful insights from the measurement data, which can be used to improve product design, optimize manufacturing processes, and enhance overall product quality.
In conclusion, the Vertical Light Path Vision Measurement System represents a significant advancement in the field of precision measurement and quality control. Its ability to perform non-contact, highly accurate, and versatile measurements makes it an invaluable tool in various industries. The system's integration with automated production lines and its user-friendly design further enhance its appeal, making it a critical component in modern manufacturing and scientific research. As technology continues to evolve, we can expect these systems to become even more sophisticated, offering even greater precision, speed, and functionality in the years to come.
Specifications:
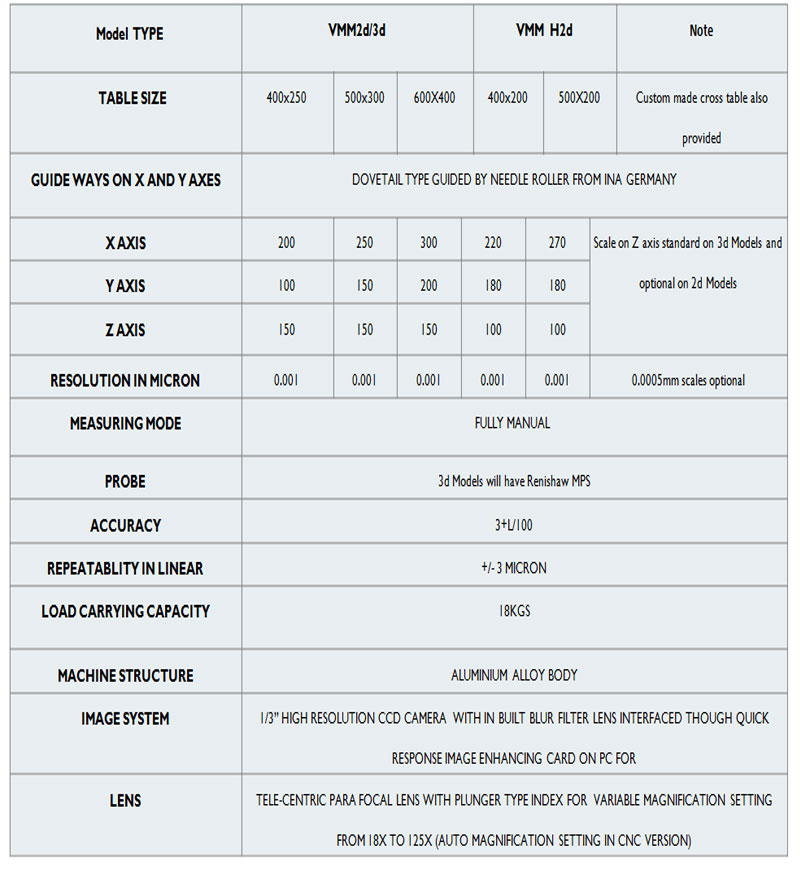